Just as technology is making our cars and our homes “smarter”, it is also transforming traditional maintenance into becoming predictive instead of just preventative. This is allowing manufacturing facilities to run leaner and gain a competitive advantage.
Instead of conducting maintenance through planned shut-downs, which limit productivity and efficiency, sensors allow maintenance to be done in an entirely different way. With Parker SensoNODE sensors and Voice of Machine™ software, plant managers can:
- set up baseline performance levels on key pain points,
- seamlessly monitor process parameters,
- see changes in machine health as they develop, and
- see histories and trends to visualize and better understand upcoming issues.
The result is a well-executed predictive maintenance program that produces more higher quality products, more consistently, with less cost.
See how the benefits can provide value for you:
- Less downtime = More production time. Keeping machinery running means more output and less backlog – and we all know that leaner operations are the name of the game in today’s manufacturing. Instead of shutting down machines according to an arbitrary timeframe that could be premature or unnecessary, machines are shut down when the data shows it is warranted.
- More data = More time to react to changing conditions. Whether it is varying chemistries, temperatures, humidity levels or some other condition that is critical to quality production, sometimes even a slight change can cause a problem. Sensors can continuously monitor conditions to be able to identify when something might be going askew so that a catastrophic event can be avoided.
- Better accuracy = Less waste. With traditional maintenance, it is possible that parts with useful service life are being thrown away. Condition monitoring enables maintenance engineers to see how much utility still exists to get the most value out of parts that can be expensive to replace.
- More readings = Higher quality product. Sensors can take more readings than labor-intensive manual monitoring. More readings means more time to catch a problem before it creates a faulty product. Less faulty product means fewer reworks and less chance of a shipment going out that could damage your reputation.
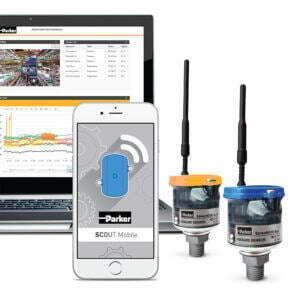
Parker SensoNODE
Parker’s SensoNODE condition monitoring sensors utilizing VOM Software are designed to help you advance maintenance to a next generation predictive maintenance plan. RitterTech and Parker can help you assess your most critical pain points to properly and continuously assess the health of your machines, allowing you to have gain a competitive advantage over other industrial manufacturing facilities.
Don’t wait to learn more about this technology. Click below to set up a site survey with RitterTech today.
So what is the best system for you and your operation? Is the expense of purchasing this type of system cost-effective for you? How will you get the data and will you be able to easily understand when you need to act? This is where RitterTech can help. There are numerous options available for to assist you in diagnosing problems, helping you maintain your equipment to prevent shut downs, and on a higher level, help you monitor your equipment on a regular or continuous basis so that you can keep it running at peak performance. As an authorized distributor for Parker products, we can assess your operations and identify the best solution to meet your needs and goals in a way that meets your budgetary restraints.