Precision, uptime, and compliance are non-negotiable for industrial processing and filtration operations.
While cross-department coordination is essential for a rapid recovery, persistent supply chain disruptions often undermine these efforts. Calling the experts for supplies, consulting and services can help you achieve maximum uptime.
MCE specializes in liquid and gas process filtration, serving oil and gas refineries and industrial operations with robust filtration solutions. Whether addressing emergencies or planned maintenance, we help clients reduce downtime, maintain compliance, and make smarter filtration decisions. Here’s how:
Join the MCE email list to get more articles like this.
More Than Process Filtration Products: A Consultative Approach
Filtration performance depends heavily on factors like environmental conditions, fluid type, and particle size—and it directly impacts your safety, efficiency, and bottom line. That’s why we take a consultative approach.
Even if processes appear similar, no two refineries are exactly alike. Onsite consultation allows us to understand your specific needs, assess current filtration setups, and uncover opportunities to improve runtime, media performance, or operational costs.
Filtration isn’t one-size-fits-all. It’s a science—and often, legacy habits like sticking with the same micron rating for years can hold you back. A small adjustment can unlock significant gains in efficiency and cost savings.
If a better solution is identified, we’ll support the Management of Change (MoC) process to help implement it across your operation.
One Purchase Order, Multiple Lifelines for Refinery Turnaround Support
When emergencies arise—such as unexpected outages or depleted filter inventory—MCE’s in-stock products and fast response times offer a lifeline.
We understand that MoC, while essential for safety and compliance, can pose a challenge for companies looking to switch vendors or products. It often requires extensive documentation, internal approvals, and, most importantly, time—a resource that may be scarce. To ease this burden, we can assist with the MoC process, even completing the documentation on the client’s behalf.
Moreover, MCE's integrated solutions— fluid power, flow control, rotating equipment, automation, filtration or inventory management—means you can get expert support and collaborative solutions from the same team.
Zone Stores for Fast, Local Access to Process Filtration Supplies
Whether it’s a planned outage or an emergency event, having product on the shelf is the key to getting back online.
Our priority is to meet the customers’ needs through supplier network of top-rated manufacturers or sourcing a specific part and/or recommending a more effective alternative. This flexibility helps us tailor the right solution for you. We do this through value-added services like our Zone Stores.
Zone Stores are customer-managed inventory solutions supported by MCE.
This program is designed to ensure quick, local access to essential filtration products while offering the convenience of onsite stock control. Benefits include:
- Faster response time
- Fewer emergency orders
- Improved usage tracking
- Reduced emergency orders and spot buys
- Enhanced visibility into inventory usage
Knowing that you have access to critical inventory via an MCE Zone Store to respond quickly to an unplanned outage provides assurance that your plant can be up and running quickly.
Cost Savings Through Industrial Filter Refurbishment
We help refineries reduce costs and avoid downtime by offering specialized services, such as cleaning metal filters and replacing media when possible, and refurbishing of radial fin filters. Filter refurbishment is particularly valuable for radial fin elements in dust collection and air handling.
Instead of replacing the entire filter, customers can send us their used elements. Our team will remove the clogged media and install a new “slip-on” filtration layer while preserving the metal core. Since the core is the most expensive component of the filter, this approach allows customers to recover and reuse valuable components rather than purchasing new filtration elements, saving up to 50% on costs.
How it works:
Before refurbishment begins, filters are inspected for contamination. If hydrocarbons are present, customers may be required to remove the media. In other cases, MCE performs cleaning and minor repairs to the inner core, such as correcting rust, corrosion, or bends. Once repairs are made, new filter media is installed, extending the filter’s lifespan at a significantly lower cost.
Note: These services are conducted at the Lake Charles manufacturing facilities and are geared toward cost savings and sustainability for customers.
If you need new filter elements, we offer and stock a variety of OEM and alternative filtration elements. We also support runtime optimization by offering modified filter media to improve longevity.
>> 10 Best Practices for Industrial Filtration Solutions in Oil & Gas Industry
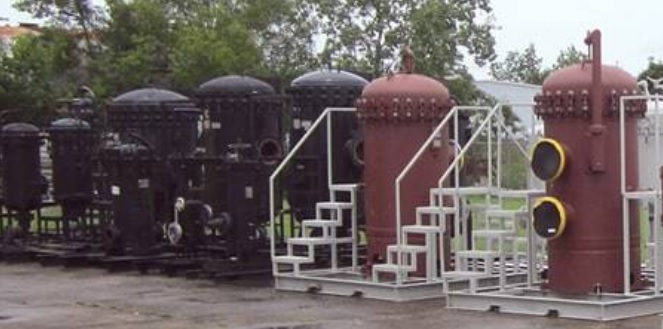
Rental Filter Vessels for Planned Maintenance
A rental vessel is a temporary, physical filtration housing unit, often mounted on a skid for portability and designed to hold replaceable filter elements. We offer rental filtration vessels needed for common scenarios, including:
- Proof-of-Concept or Trials: Customers may rent vessels for trial runs to see if a filtration step solves an issue before committing capital for a permanent system. If successful, they might buy the same vessel, or the right-sized version based on actual needs.
- System Upsets: Sudden contamination, pressure drops, or other processing irregularities may require temporary filtration support. Rental vessels are available to provide filtration and reduce changeout intervals.
- Planned Outages: For planned outages where the circulation system is down for maintenance, a pump and rental vessel can be used in a "kidney loop" to continuously circulate and clean the liquid (e.g., dirty amine streams, quench water, etc.) to streamline restart.
- Tank or Barge Cleanouts: Used to filter out hydrocarbons and solids from fluids drained from tanks or barges. It helps customers avoid costly disposal by allowing clean water to go to municipal treatment instead of hazardous waste.
Why Use Rental Vessels:
Rental vessels help customers avoid capital expenditure and use existing maintenance and operations budgets instead. Renting provides refineries with a fast response when engineering approvals for permanent installations are delayed. Also, placing a rental vessel at your location helps businesses comply with environmental and discharge regulations.
How the Process Works:
>> Learn more about MCE’s rental filter vessels
Note: MCE rents the standalone vessels, and customers are responsible for installation. MCE's integrated solutions can also provide pumps, valves, gauges, filters, hoses, connections, and other installation needs.
MCE is your Consulting and Emergency Service Provider
Your filtration needs don’t stick to business hours. If you’re burning through filters because of a process upset, we’re always on-call, assisting you during urgent situations.
Getting you back online isn’t just our business model; it’s a business practice built for plants that never stop running. If a customer needs a 10-micron filter but we only have 20-micron in stock—we’ll do what we have to do to get them up and running. Whether it’s a late-night emergency or helping a customer transition to a better filtration system, we’re on your side 24/7.
From cost-saving filter refurbishments and responsive emergency support to consultative guidance and vendor-neutral sourcing, we promise more than just parts—we promise peace of mind. And we have the expertise to back it up.
In an industry built on precision, risk management, and uptime, success goes beyond having the correct part numbers. It’s about having the right people—and the right partner—at exactly the right time.
Contact us to get a free assessment on your plant’s needs.